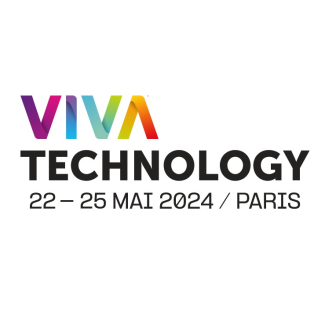
Research comes together around the 3D printing of metal and ceramics
• High Energy Additive Manufacturing uses 3D printing to create original metal and ceramic objects, such as lightweight structures with properties that are unattainable using traditional processes. |
The 3D printing of metal and ceramics is used today in numerous industrial sectors (such as transportation, the space and biomedical industries, and defence). It produces objects with novel properties that cannot be attained using traditional processes. However, numerous barriers remain, especially to achieve better control over the new properties of alloys formed in this way. Thirteen laboratories from the CNRS and its partners, in addition to a department from ONERA, have come together for a 5-year period to create a scientific interest group to tackle these issues.
Additive manufacturing is any process that produces—layer by layer through the addition of material—a physical object based on a digital object. It includes a wide range of materials and uses, ranging from wire polymer to metal powder. A most recent example is the application of additive manufacturing processes to the ceramics and metals that use high energy sources (such as lasers or electron beams) to melt materials. They emerged in the early 2000s, and are now experiencing significant growth in terms of industrial applications and investment.
The aim of the “High Energies in Additive Manufacturing” scientific interest group (GIS Head) is to fully participate in the accelerated industrialization of these new technologies. The group’s goal is to improve the performance of additive manufacturing across the entire value chain, from developing and simulating the initial digital object to controlling for the final object’s microstructures and defects (surface imperfections, porosity, lack of fusion, grain size, texture, etc.), for instance in the composition of powders, wires, and filaments. The group is positioned in relation to the must fundamental issues and barriers1 , always with a view to maturation and industrial use, consistent with its regional and national partners.
The launch of GIS Head will be accompanied by the creation of an industrial club whose members will have preferred access to technical meetings and regular expertise, in addition to priority access to the intellectual property generated by the GIS.
This new GIS includes the following laboratories:
- Centre for Materials (CNRS/Mines Paristech)
- Centre for Materials Forming (CNRS/Mines Paristech)
- Centre for Applied Mathematics (CNRS/Ecole polytechnique)
- Research Institute in Civil and Mechanical Engineering (CNRS/Université de Nantes/Ecole Centrale de Nantes)
- Bordeaux Institute of Mechanics and Engineering (CNRS/Université de Bordeaux/Arts et métiers sciences et technologies/Bordeaux INP)
- Georges Friedel Laboratory (CNRS/Mines Saint-Etienne)
- Solid Mechanics Laboratory (CNRS/Ecole polytechnique)
- Gas and Plasma Physics Laboratory (CNRS/Université Paris-Saclay)
- Automated Production Research Laboratory (ENS Paris-Saclay/Université Paris-Saclay)
- Processes and Engineering in Mechanics and Materials Laboratory (CNRS/Cnam/ Arts et métiers sciences et technologies)
- Materials and Process Science and Engineering (CNRS/Université Grenoble Alpes/Grenoble INP)
- The Materials, Science, Engineering Laboratory (CNRS/Insa Lyon/Université Claude Bernard Lyon 1)
- ONERA Materials and Structures Department
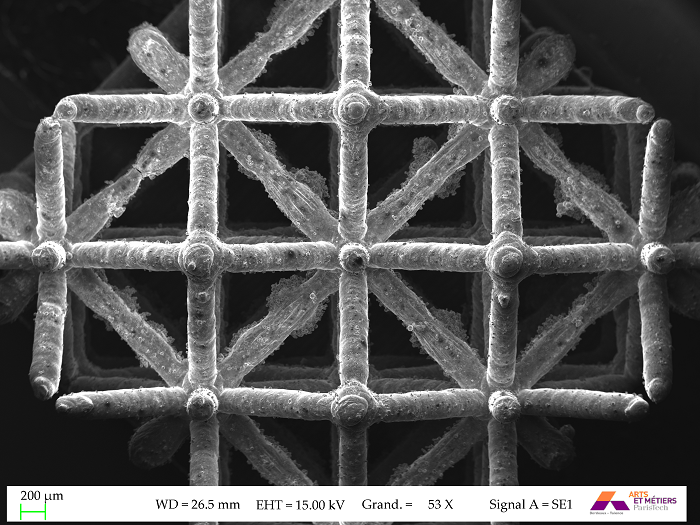
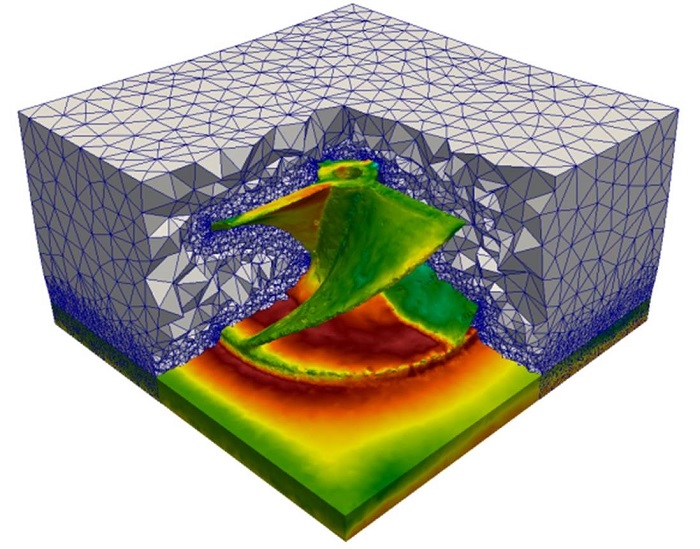
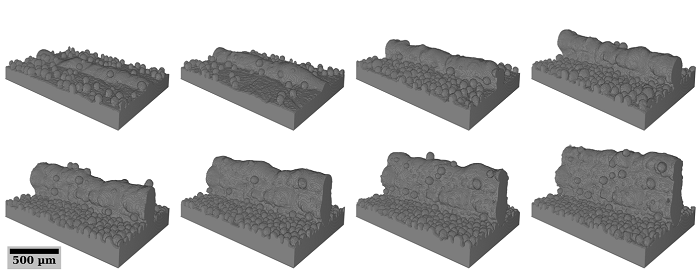
- 1From 1 to 3 on the TRL scale, a measurement system used to assess a technology’s level of maturity. The first three levels involve the description of basic principles, technological concepts, and analytic or experimental proof of the concept’s primary characteristics.